Toyota has led the innovation of sustainability in the automotive industry for decades. From launching the first mass-produced hybrid vehicle in 2000 to opening the first Net Zero ready car dealership in the world sixteen years later, one thing is clear: Toyota knows how to go green.
Built by R&H in 2016, Toyota of Corvallis is a commercial automotive project that includes construction of a showroom, service facility and inventory lot for Toyota and Subaru. The phased project schedule allowed the car dealership to remain open and fully operational throughout the entirety of the near two year project duration. The 1-story, 34,868 s.f. building is situated on a 137,400 s.f. site on Northwest 5th Street in Corvallis, Oregon. The project is LEED Platinum certified and was the first Net Zero car dealership in the world.
Phased & Occupied Construction
Toyota of Corvallis (TOC) was completed in three phases which allowed the car dealership to remain open throughout the project.
Phase I included the conversion of a gravel lot into an inventory storage lot. As a part of sustainability efforts, pervious asphalt paving was utilized on the lot, allowing rainwater to drain through the asphalt and back into the subgrade. This phase of the project also included installing LED lighting and landscaping in the lot.
The second phase of the project occurred on the most northern section of the project site. Teams demolished the existing parking lot before beginning construction of the north half of the new building; which would serve as the new service and mechanic shop. The 16,778 s.f. building is a combination of CMU and metal stud framing with composite metal panels and curtain wall. Inside is a full service shop featuring 18 service stalls and two carwash bays. After finishing the building, pervious asphalt was installed on the remaining parking lot. When this phase of the project was complete, TOC service employees moved into their new space resulting in no lost time for the shop. At this time, R&H also set up temporary trailers and moved Toyota of Corvallis’ office and employees into temporary trailers that remained operational through the final phase of construction. Working on a fully occupied site and keeping the dealership open created several obstacles throughout the course of the project however R&H was able to overcome the challenge while maintaining both safety and schedule.
Demolition of the existing building and construction of the showroom made up the final 10-month phase of construction. The 18,090 s.f. showroom features 12 glass-walled offices, a break room and a 40-person training room. Finishes include a 9Wood ceiling, ceramic floor tiles and an 8’x60’ magnetic timeline, signature to Toyota dealerships, featuring Corvallis specific artwork. The exterior of the building is made up of ACM panels the iconic Toyota red band and Novum illuminated glass portal. Phase III of the project also included the installation of aluminum canopies and the construction of the covered service lanes.
Net Zero & LEED Platinum Certification
The Toyota of Corvallis project is one of a kind. Not only is it Toyota’s few dealerships to achieve LEED Platinum certification but it is the first Net Zero ready car dealership in the world. The building features many sustainable elements including a rooftop PV panel energy farm, geothermal wells and a 37,000 gallon rainwater collection cistern.
During phase II, crews also began the 7-week process of digging geothermal wells to feed the radiant heat flooring. After initial testing, engineers discovered they would need to dig 18 wells, instead of the planned 14, in order to generate the heat needed. The wells were drilled to 300’ feet in depth resulting in over 3 miles of piping used to complete the system. The efficiency gained from geothermal heating allows for minimal power usage by utilizing natural energy as the heating element in the system. This system further contributes to the movement of environmental sustainability that Toyota is known for.
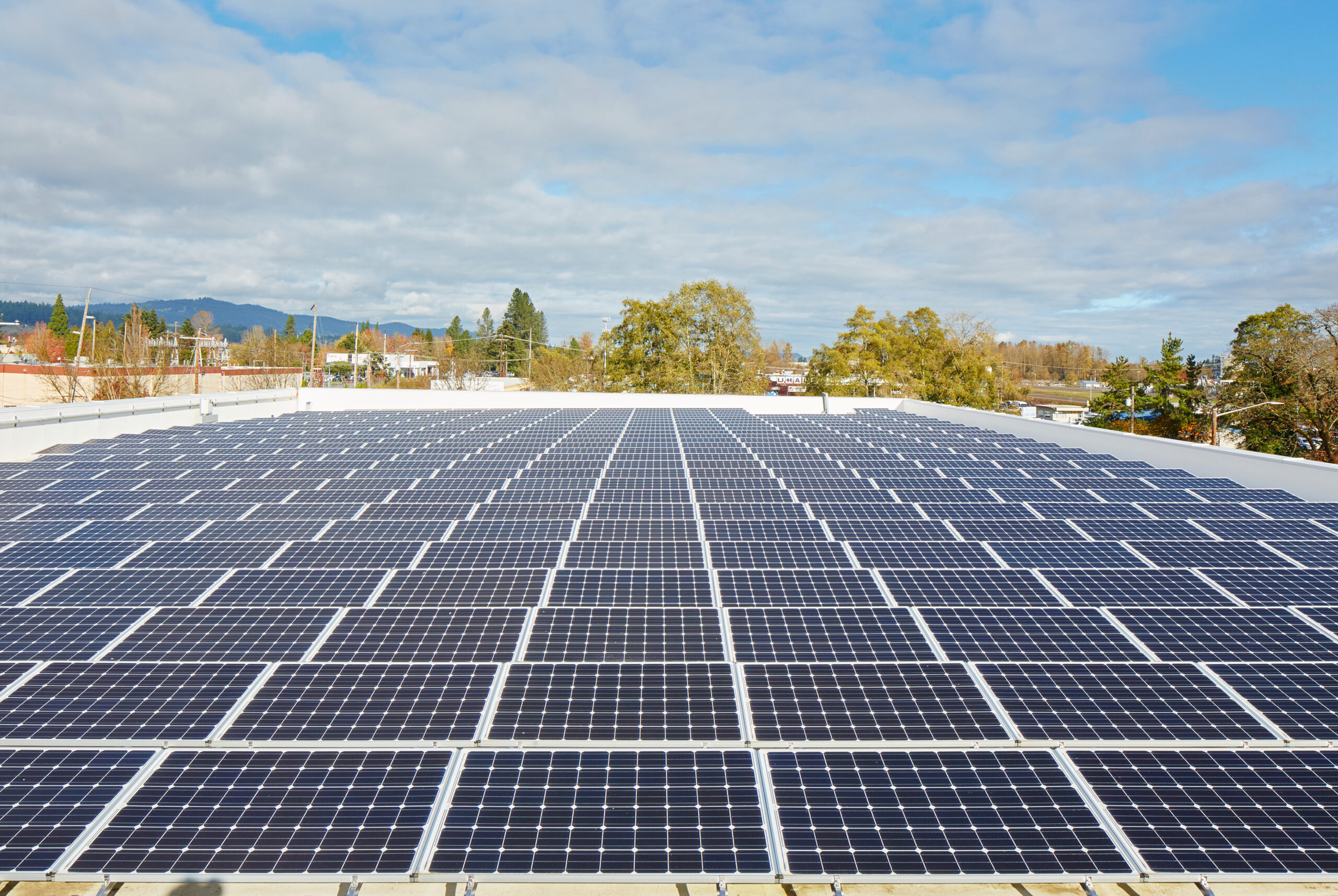
How The Building Produces More Energy Than It Consumes
Atop the TPO roof sits an array of 1,025 PV panels, each comparable in size to 50” TV screens. Collectively, these solar panels are able to generate 298,000 KW of energy per year, which is the approximate consumption of 30 residential homes. This amount of energy ended up creating a challenge for the TOC team, as PP&L, the local electric company, had infrastructure that was unable to handle the amount of power Toyota’s solar panels would be feeding back into the system. As a result, PP&L required Toyota to pay for the facility upgrade in order to allow them send power back into the grid. R&H’s project team coordinated with PP&L to install a fiber optic line from the project’s solar ‘brain’ to a pole near the property corner that connects to the offsite substation, located over the railroad and across a creek. The line allows the PP&L substation to effectively shut-off TOC power supply to them in the event of a problem. Installation of this fiber optic line also resulted R&H’s teams managing new easements and permits with the railroad and other jurisdictions.
Sustainable Solutions: A Rainwater Cistern, CO2 Sensor System, and More
The TOC project includes several other sustainable elements including a rainwater cistern, CO2 Sensor System and intricate building management system. The 37,000 gallon rainwater cistern collects rainwater to be used in the dealership’s landscape drip irrigation system. The building’s CO2 sensor system tracks CO2 levels in the service building. When the CO2 reaches a level the sensor deems unsafe, large 16’ fans turn on and the coiling doors open to exhaust the CO2 buildup. This, in combination with low VOC building materials, allows the building to maintain high indoor air quality at all times. TOC’s building management system services the hub for all building systems. From mechanical and electrical to lighting and some plumbing, the system monitors and meters 13 different points of the building’s energy usage and creates reports that can be viewed by employees and clients in the dealership showroom. Other sustainable elements of the project include low-flow plumbing fixtures, 100% LED lighting and timer controlled electrical outlets. The outlets turn off at the end of the day to eliminate dormant energy use during the dealerships’ closed hours.
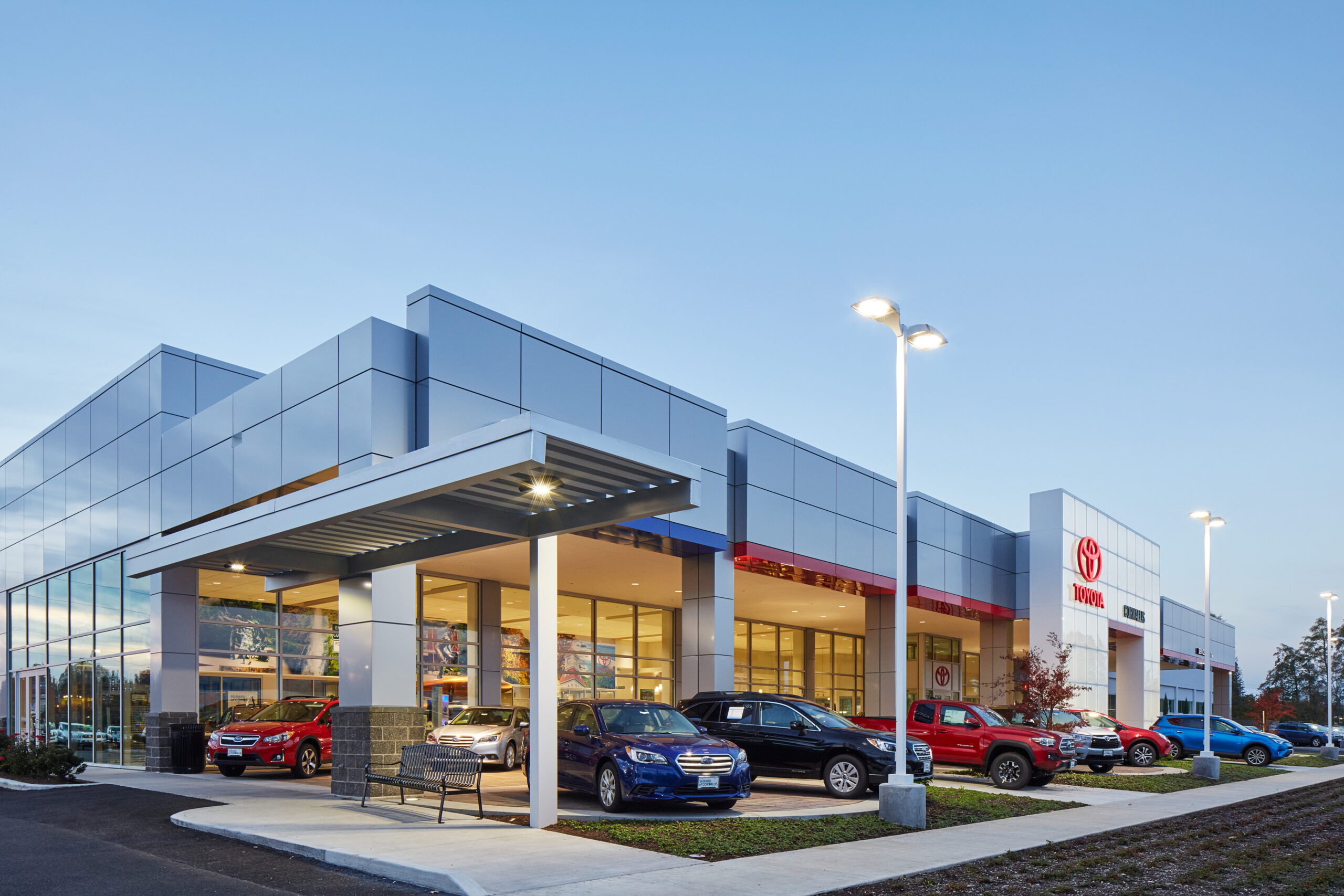